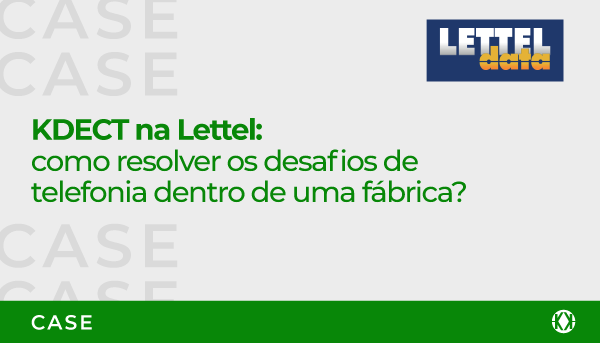
Is it possible to ensure that a hydraulic cylinder industry located in Carazinho (RS) – a city with around 60,000 inhabitants – keeps its telephone system running without interruptions, even in the midst of heavy machinery and with high mobility among engineers and workers in the factory corridors?
This was the question that started the project supported by Lettel Data, a company that has been serving complex corporate communication demands since the early 1990s. The challenge was to combine its Convert solution, an IP platform based on Asterisk, with a high-coverage telephone system in the midst of a completely challenging scenario.
In addition to the factory floor, we also needed to serve other areas of the company, from the production team to HR. The demand was to unify everything, without losing the quality of internal or external calls – highlights Bruno Amaral, technical consultant at Lettel.
The project’s success came with the KDECT line, Khomp’s multicellular communication system. Check out details of the implementation:
First challenges encountered
During the first visits to the factory, it was noticed that the scenario consisted of an analog PABX, without any management or practicality beyond the basic combo of “making, receiving and transferring calls”. Mobility was almost non-existent. There were more than 30 telephones spread throughout the company, all connected to individual points, without any connection between them.
After carrying out a detailed study, we found that we could not offer a conventional cordless telephone network, as coverage is limited to the range of the base. Nor could we offer Wi-Fi devices, because call quality is almost always a problem in industrial environments.
Among the market offerings, the best one found by the Lettel team was the KDECT Line from Khomp. The decision was based on some crucial factors: ease of IP and SIP networks, compatible with the Convert platform that would be used in the project. And the DECT technology itself, which offers greater stability, reliability in implementation and facilities such as handover and roaming.
Being able to count on Khomp’s full support, both in terms of engineering and support, was another very important differentiator in the choice. In addition to being a supplier, they were true partners throughout the process.
Hassle-free implementation
The complexity of a DECT system is a feature that has always deserved special attention. However, when properly supported and guided, it can be easily overcome.
The deployment went much more smoothly than we expected. In one shift, we connected the 3 bases, 1 repeater and registered 20 handsets (cordless phones). The roaming and handover configuration is automatic, everything worked after the initial configuration.
Unexpected results
The hydraulic cylinder industry now has its telephone system entirely based on mobility and performance. The new KDECT equipment met expectations by delivering modernity, durability and a very noticeable quality when compared to previous equipment.
It is gratifying to see factory supervisors being able to monitor processes from one corner of the factory to the other, knowing that they will always be able to receive or make calls. The areas without coverage have disappeared.
Furthermore, according to Bruno, there was widespread acceptance across all areas of the company. In addition to enjoying full coverage, users began to use new features more easily, such as an integrated calendar and conference room. Both features were offered by the Convert platform in conjunction with the KDECT Line.
In the end, not only was the telephone system changed, the project renewed elements of the company’s culture.
Want to know more about the KDECT Line?
To learn about all the features of the KDECT Line, consult the product page and/or our Sales Consultants.
Subscribe to the Khomp newsletter to receive other articles on technologies that can help your telephony project.